The world of manufacturing has been revolutionized by the advent of 3D printing technology. What started as a method for creating plastic prototypes has now evolved into a sophisticated process that can produce intricate metal structures with unparalleled design flexibility. The use of metal 3D printing, also known as additive manufacturing, has seen a significant rise in various industries, from aerospace and automotive to healthcare and jewelry making.
While the benefits of this cutting-edge technology are undeniable, the question remains: what is the true cost of metal 3D printing? In this article, we will delve deep into the financial landscape of metal 3D printing, exploring the various factors that influence its cost and analyzing the potential returns on investment for businesses embracing this innovative technology. So let’s dive in and navigate the cost maze of metal 3D printing.
Types of Metal 3D Printers
Before we delve into the cost breakdown, it is essential to understand the different types of metal 3D printers available in the market. There are three main types of metal 3D printers:
Powder bed fusion (PBF)
PBF is the most commonly used metal 3D printing technology. It utilizes a high-powered laser or electron beam to fuse layers of powdered metal together to create a solid object. This process can produce intricate designs with high accuracy and is suitable for a wide range of metals, including titanium, aluminum, and stainless steel.
Directed energy deposition (DED)
DED involves using a laser or electron beam to melt metal powder or wire and deposit it onto an existing structure to build up the desired shape. This process is faster than PBF but is limited in terms of precision and the types of materials that can be used.
Binder jetting
Binder jetting involves spraying layers of metal powder with a binding agent to bind them together and create a solid object. This process is suitable for producing large and complex parts but results in a lower density and weaker final product compared to PBF or DED.
Now that we understand the different types of metal 3D printing technologies let’s explore the factors that influence the cost of this technology.
Factors Affecting Metal 3D Printer Cost
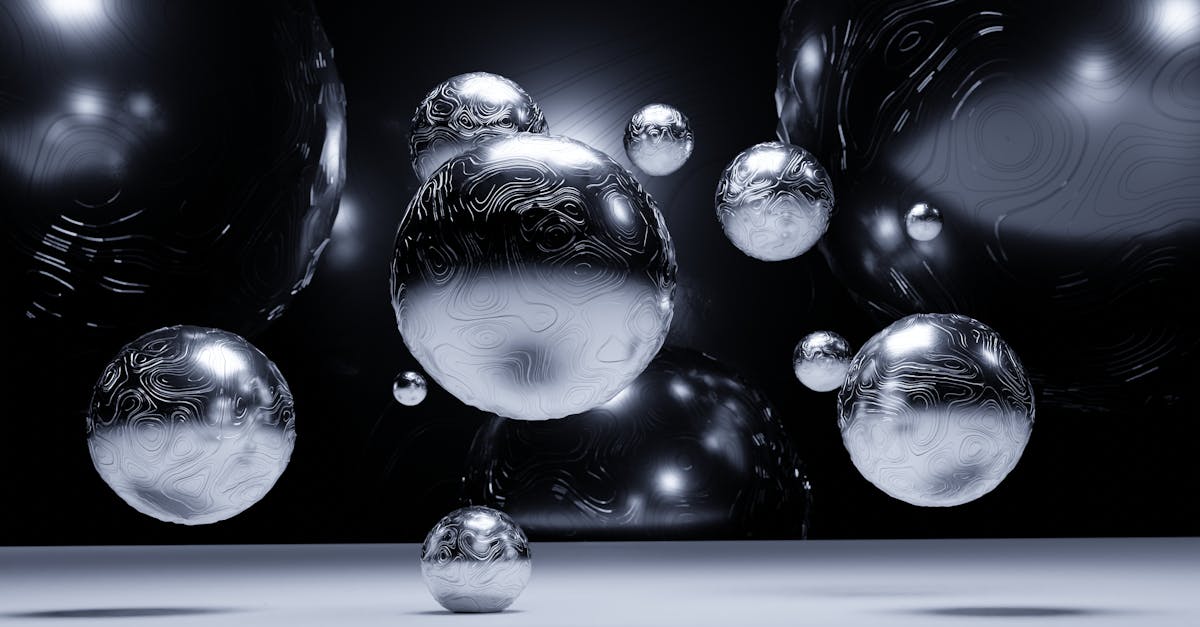
The cost of metal 3D printing is a complex equation with numerous variables. Unlike traditional manufacturing methods, where costs are relatively straightforward, metal additive manufacturing presents a unique set of factors that influence the bottom line. Let’s look at these factors in more detail:
Initial Investment Costs
The initial investment in a metal 3D printer can range from tens of thousands of dollars for entry-level models to millions for industrial-grade machines. This is a significant initial hurdle that not all businesses can easily overcome. Additionally, there are other associated costs such as software, materials, and training that need to be factored in.
Operating Costs
Operating costs include the expenses incurred during the actual production process, such as electricity, gas, and labor costs. These costs can vary depending on the type of metal 3D printer used and the complexity of the design being printed. For example, PBF technology requires a high-powered laser, which translates into higher electricity and maintenance costs compared to binder jetting.
Maintenance Costs
Like any other machine, metal 3D printers require regular maintenance to perform optimally. This includes routine checks, part replacements, and software updates. The frequency and extent of maintenance can vary depending on the type and usage of the printer. It is essential to factor in these costs when considering the overall expense of metal 3D printing.
Materials
One of the significant advantages of metal 3D printing is the ability to use a wide range of materials, including exotic alloys. However, the cost of these materials can significantly impact the overall cost of production. For example, titanium is an expensive material compared to steel, and using it for printing will significantly increase the cost of production.
Post-Processing
Post-processing refers to any additional steps required after the printing process is complete. This can include removing supports, polishing, or heat treating the final product. These costs can add up, depending on the complexity of the design and the desired finish.
Comparison of Different Metal 3D Printer Costs
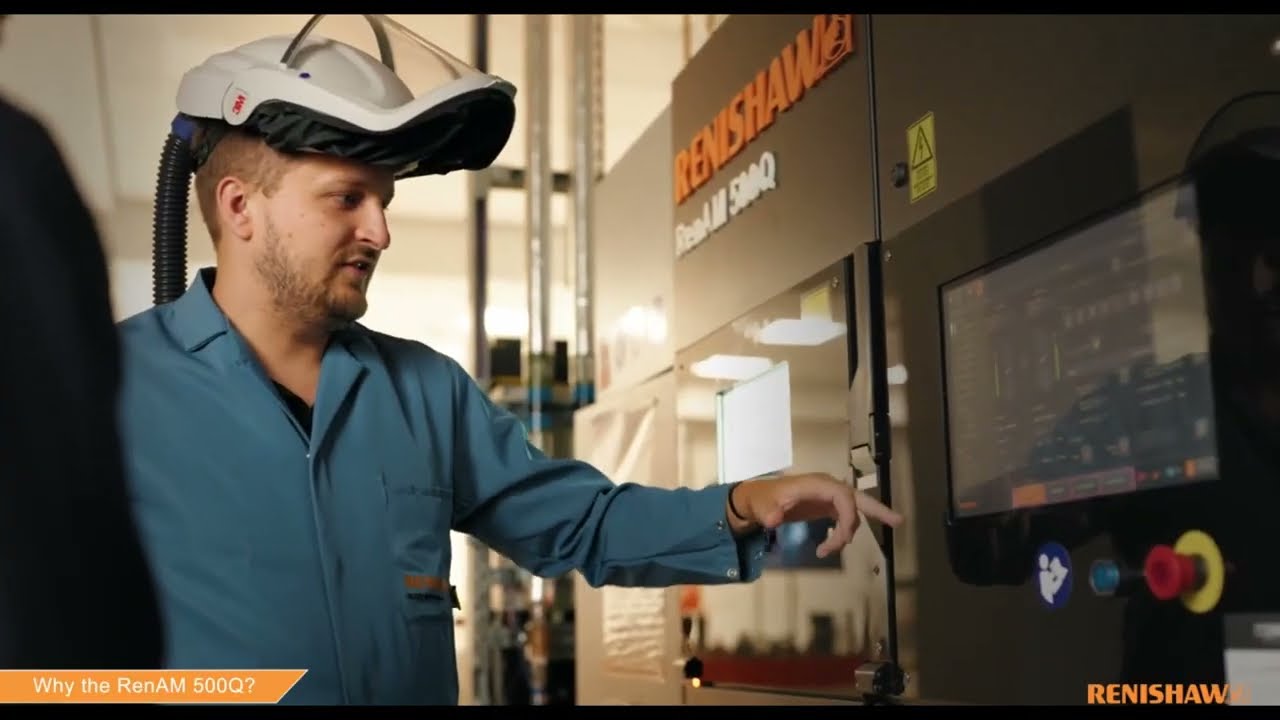
As mentioned earlier, the cost of metal 3D printing can vary depending on various factors. To get a better understanding, let’s compare the cost of different metal 3D printers in terms of initial investment and operating costs.
Type of Printer | Initial Investment | Operating Costs |
---|---|---|
PBF | $100,000-$2 million | High |
DED | $200,000-$500,000 | Medium-high |
Binder Jetting | $50,000-$150,000 | Low-medium |
The initial investment for PBF printers is significantly higher than both DED and binder jetting. However, PBF also offers the highest precision and range of materials, making it a preferred choice for industries that require high-quality metal parts. DED has a slightly lower initial investment cost compared to PBF but may require more extensive post-processing, resulting in higher overall costs. Binder jetting has the lowest initial investment cost but is limited in terms of accuracy and material options.
Tips for Reducing Metal 3D Printer Costs
While metal 3D printing can initially seem expensive, there are ways to reduce costs and make it a viable option for businesses. Here are some tips to help you cut down on metal 3D printing expenses:
Plan Your Designs Wisely
The complexity of your design plays a significant role in determining the cost of production. By simplifying your design and reducing the number of supports needed, you can reduce material usage and post-processing costs.
Optimize Material Usage
Reducing the amount of material used in the printing process can significantly impact overall costs. This can be achieved by using lattice structures or hollow designs, which not only use less material but also result in a lighter final product.
Utilize Your Printer’s Full Capacity
To make the most out of your initial investment, it is crucial to fully utilize your printer’s capacity. This means planning and producing multiple parts in each print run, which reduces per-part printing costs.
Explore Different Material Options
While exotic materials may offer unique properties, they come at a high cost. It is essential to explore different material options and choose the one that best fits your requirements and budget.
Conclusion
Metal 3D printing has undoubtedly revolutionized the manufacturing industry, offering unparalleled design freedom and rapid prototyping capabilities. However, it is crucial to understand the various factors that influence the cost of this technology to make an informed decision. From initial investment and operating costs to material and post-processing expenses, every aspect plays a role in determining the overall cost of metal 3D printing. By understanding these factors and following the tips mentioned above, businesses can reduce costs and reap the benefits of this innovative technology.